FAQ
Helpful Q&A
Got questions about Stealth or our solutions? Dive into our FAQ page, where we’ve tackled the most common questions about our products, technologies and services. The world of rugged computing can be a complicated one, but we’re here to help!
Reach out if you require additional answers at: [email protected]
Don’t see the answer to your question? Talk to our Chat Bot at the bottom of the page!
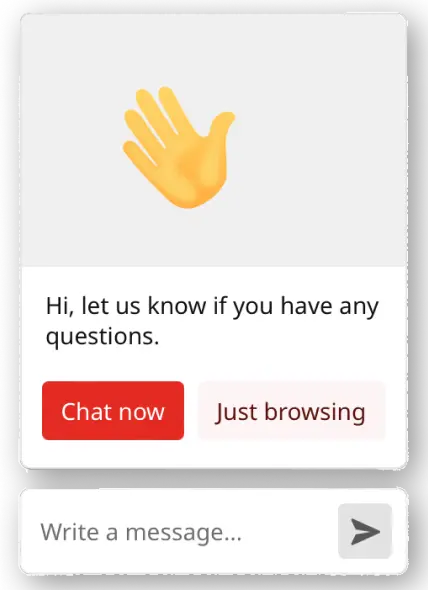
Product
Sales & Shipping
General
Products
Little PCs/Rack PCs & Servers
1. What is a Rugged Industrial Little PC?
2. What are the typical applications for Rugged Industrial Little PCs?
3. What makes Rugged Industrial Little PCs different from regular desktop computers?
4. Are these Little PCs resistant to dust and moisture?
5. Can I use a Rugged Industrial Little PC in extreme temperatures?
6. Do Rugged Industrial Little PCs support wireless connectivity?
7. What kind of expansion options are available on these Little PCs?
8. How do I choose the right Rugged Industrial Little PC for my application?
9. Can I run standard operating systems and software on these Little PCs?
10. What is the expected lifespan of a Rugged Industrial Little PC?
11. Are these Little PCs customizable to meet specific requirements?
12. How can I ensure the security of data stored on these Little PCs?
13. What kind of technical support and warranty options are available?
14. Can these Little PCs be integrated into existing industrial systems easily?
15. What is a “U” or more specifically in a “Rack Mount PCs & Servers”?
A “Rack Unit” or “U” is an Electronic Industries Alliance or more commonly “EIA” standard measuring unit for rack mount type equipment. A “Rack Unit” is equal to 1.75″ in height. To calculate the internal usable space of a rack enclosure you would simply multiply the total amount of Rack Units by 1.75″. For example, a 4U rack enclosure would have 7.0″ of internal usable space (4 x 1.75”).
Stealth manufactures products that are designed to fit into standard EIA size rack enclosures. Stealth’s Rack Mount PCs, Displays/Monitors, KVM DIsplays and Keyboards are available in many sizes and configurations. The slim space saving series rack products are available in 1U (1.75″) and 2U (3.5″) in overall height. Since rack space is at a premium these slim products represent significant cost savings to the end user. Standard rackmount products are available in 1U, 2U, 3U and 4U configurations.
16. My Rugged Industrial PC is not powering on. What should I do?
17. The screen displays a blank or black screen. How can I resolve this?
18. My Rugged Industrial PC is running slowly. How can I improve its performance?
19. I'm experiencing intermittent connectivity issues with my Rugged Industrial PC. What could be the cause?
20. My Rugged Industrial PC is producing unusual noise. Is this normal?
21. My Rugged Industrial PC is overheating. What steps should I take to prevent this?
22. The operating system on my Rugged Industrial PC is experiencing stability issues. How can I address this?
23. I've forgotten the BIOS or system password for my Rugged Industrial PC. What should I do?
24. My Rugged Industrial PC is displaying error messages during startup. How can I troubleshoot this?
25. The data on my Rugged Industrial PC is corrupted or inaccessible. How can I recover it?
26. How can I perform a factory reset or restore my Rugged Industrial PC to its default settings?
27. Can I upgrade the hardware components (e.g., RAM, storage) in my Rugged Industrial PC?
28. My Rugged Industrial PC is still under warranty and experiencing issues. What should I do?
29. How can I ensure the long-term reliability of my Rugged Industrial PC?
Regularly perform preventive maintenance, keep the system clean, and follow manufacturer-recommended guidelines for usage and environmental conditions. Create backups of critical data to avoid data loss.
These troubleshooting FAQs should assist you in resolving common issues with Rugged Industrial PCs and provide guidance on when to seek professional support. Feel free to reach out to our support team for professional help at [email protected] or submit our case on our website. Contact us online
Displays/Monitors
1. What are rugged industrial Displays/Monitors?
2. What makes industrial Display/Monitors "rugged"?
3. Where are rugged industrial Display/Monitors typically used?
4. What are the advantages of using rugged industrial Display/Monitors?
Reliability: They provide consistent performance in challenging environments.
Longevity: Rugged displays have a longer lifespan compared to consumer-grade Display/Monitors.
Safety: They are often designed to meet safety standards and certifications.
5. Are rugged industrial Display/Monitors customizable?
6. Can rugged industrial Display/Monitors be used in outdoor environments?
7. Do rugged industrial Display/Monitors support touchscreen functionality?
8. Are rugged industrial Display/Monitors compatible with industrial PCs and systems?
9. What certifications or compliances should I look for in rugged industrial Display/Monitors?
10. How do I maintain and clean rugged industrial Display/Monitors?
11. What mounting options are available for rugged industrial Display/Monitors?
Rugged industrial Display/Monitors offer various mounting options to suit different installation requirements. Common mounting options include:
Panel Mount: These Display/Monitors are designed to be mounted flush with a control panel or enclosure, providing a sleek and integrated appearance. Panel-mount Display/Monitors are often secured using mounting clips or bolts.
Desktop/VESA Mount: Rugged Display/Monitors with VESA (Video Electronics Standards Association) mounting compatibility can be attached to VESA-compliant brackets or arms, allowing for flexible placement on walls, arms, or stands.
Rack Mount: Rack-mounted rugged Display/Monitors are suitable for installation in standard server racks or enclosures. They come in various rack-unit (U) sizes.
Open Frame: Open-frame Display/Monitors lack an enclosure and are designed for integration into custom-built enclosures or machinery. They are commonly used in OEM applications.
12. Can I switch between different mounting options for my rugged industrial Display/Monitor?
In many cases, it is possible to switch between mounting options, but this may require additional hardware or brackets. Check with our sales specialist to determine the compatibility and availability of interchangeable mounting accessories.
13. Are there thermal management issues with sunlight readable displays?
14. What is a NIT?
For an LCD Display/Monitor it is brightness out of the front panel of the display. A NIT is a good basic reference when comparing brightness from Display/Monitor to Display/Monitor. Most desktop LCD’s or Notebook LCD’s have a brightness of 200 to 250 Nits. These standard LCD’s are not readable in direct or even indirect sunlight as they become washed out. Stealth offers a range of sunlight readable Displays for use in areas of high ambient light.
15. How do I know how many NIT’s I require for my application?
16. How do I select a Touch Screen Technology for my Display/Monitor?
17. Display/Monitor Won't Power On:
- Check if the power cable is securely connected to both the Display/Monitor and the power source.
- Verify that the power source is working correctly by testing it with another device.
- Look for any visible damage to the power cable or connectors.
18. No Display or Blank Screen:
- Ensure that the Display/Monitor’s brightness and contrast settings are appropriate.
- Check if the Display/Monitor is receiving a video signal from the connected source (e.g., computer, camera).
- Test the Display/Monitor with a different video cable to rule out cable issues.
- Verify that the Display/Monitor’s input source is correctly selected (e.g., VGA, HDMI, DVI).
19. Image Quality Problems:
- If the image is distorted or flickering, check the video cable for loose connections.
- Adjust the Display/Monitor’s resolution and refresh rate settings to match the source device’s capabilities.
- Inspect the source device for graphics card or output issues.
20. Touchscreen Not Responding:
- Clean the touchscreen surface to remove any dirt, dust, or debris that may be affecting touch sensitivity.
- Ensure that the touchscreen drivers are correctly installed on the connected computer.
- Test the touchscreen functionality in a different software or application to rule out software issues.
21. Physical Damage:
- Inspect the Display/Monitor for visible physical damage such as cracks, dents, or broken components.
- If there is any damage, contact the manufacturer or authorized service provider for repair options.
22. Overheating or Thermal Issues:
- Ensure that the Display/Monitor’s ventilation is not obstructed, and the cooling system (if applicable) is functioning properly.
- Display/Monitor the operating temperature of the environment and make sure it falls within the Display/Monitor’s specified operating range.
23. Interference or EMI/RFI Issues:
- Check for nearby sources of electromagnetic interference (EMI) or radio-frequency interference (RFI) and relocate the Display/Monitor if necessary.
- Use shielded cables and connectors to reduce susceptibility to interference.
24. Calibration Problems (for touchscreen Display/Monitors):
- Recalibrate the touchscreen using the manufacturer’s calibration software.
- Verify that there are no physical obstructions or damage to the touchscreen surface.
25. Software and Driver Issues:
- Ensure that the Display/Monitor’s drivers are up to date by checking the manufacturer’s website.
- Reinstall or update graphics card drivers on the connected computer if necessary.
26. Consult the User Manual and Manufacturer's Support:
- Review the user manual for specific troubleshooting steps and recommendations provided by the manufacturer.
- Contact our support team for assistance with complex issues or if the Display/Monitor is under warranty.
Remember that rugged industrial Display/Monitors are built to withstand challenging conditions, but regular maintenance and proper usage are essential to maximize their lifespan and reliability. If you’re unsure about any troubleshooting steps or encounter persistent issues, it’s advisable to seek professional assistance. You can reach us at [email protected] or submit an online case with us via our website.
Rack Mount KVM Displays
1. What is a Rack Mount KVM Displays?
2. What is the purpose of an Rack Mount KVM Display?
3. What are the key features of an Rack Mount KVM Display?
- Integrated keyboard, Display/Monitor, and mouse
- 19-inch rack-mountable design
- Support for various video resolutions
- Multiple input/output ports for connecting servers or computers
- Secure access control options (password protection, encryption)
- Compatibility with different operating systems
- Adjustable depth to fit different rack sizes
- Robust construction for durability in industrial environments
4. What are the advantages of using a Rack Mount KVM Display?
- Space-saving: Consolidates control devices into one unit, saving rack space.
- Cost-effective: Reduces the need for multiple Display/Monitors and peripherals.
- Centralized management: Allows administrators to control multiple devices from one location.
- Improved efficiency: Streamlines server maintenance and troubleshooting.
- Enhanced security: Provides secure access control options.
- Compatibility: Works with various server and computer configurations.
5. How do I install an Rack Mount KVM Display in my rack?
6. What types of video resolutions are supported by Rack Mount KVM Displays?
7. Can I switch between different servers or computers using an Rack Mount KVM Display?
8. Are there options for remote access to Rack Mount KVM Displays?
9. What security features are available to protect access to an Rack Mount KVM Display?
10. Can I connect different types of servers or computers to an Rack Mount KVM Display?
Yes, Rack Mount KVM Displays typically provide various input/output ports (such as USB, PS/2, and VGA or HDMI) to support a wide range of server and computer configurations. Compatibility may vary by model, so check the specifications.
11. What should I consider when choosing an Rack Mount KVM Display for my setup?
Panel PC (All-in-One)
1. What is an Industrial Panel PC?
2. What are the typical applications for Industrial Panel PCs?
3. What sets Industrial Panel PCs apart from regular computers?
4. What is the difference between a Panel PC and an HMI (Human-Machine Interface)?
5. What are some key features to look for in an Industrial Panel PC?
6. Can Industrial Panel PCs be customized?
7. How do you maintain and clean Industrial Panel PCs?
8. Are Industrial Panel PCs suitable for outdoor use?
9. What is the expected lifespan of an Industrial Panel PC?
10. Are Industrial Panel PCs compatible with various operating systems?
Most Industrial Panel PCs are compatible with popular operating systems like Windows and Linux. The choice of the operating system depends on your specific application and software requirements.
When considering an Industrial Panel PC for your application, it’s essential to assess your specific needs, including environmental conditions, required features, and compatibility with existing systems and protocols. Consulting with a reputable supplier or manufacturer can help you choose the right Industrial Panel PC for your industrial automation project.
Sales & Shipping
1. How can I place my order?
If ordering from within the USA or Canada, the following options are available:
- Contact your Sales Representative by Phone,
Toll Free: 1-888-STEALTH (783-2584);
Local: (905) 264-9000 - Contact your Sales Representative by Email
- Fill out our Contact Form, [email protected], and a representative will contact you
- Web Order – Visit www.stealth.com and/or www.shop.stealth.com (free shipping for order values of $1,500.00 USD / $2,000 CAD or higher)
For International customers, the following options are available:
- Contact your Sales Representative by Phone,
Toll Free: 1-888-STEALTH (783-2584) - Contact your Sales Representative by Email
- Fill out our Contact Form and a representative will contact you
A Proforma Invoice will be issued in advance for completion of your payment by Wire Transfer.
2. What payment methods do you accept for orders?
We offer you flexibility with the following:
- Credit Card Orders:
- VISA, MasterCard, American Express or PayPal orders are accepted for USA & Canada
- Apple pay, Google pay, Samsung pay and other digital wallets are available online
- Electronic Payments:
- Bank remittances – EFT, ACH or other Wire payment methods are available
- Credit Terms:
- Net 30-Day Credit Terms can be established (North America Only) by supplying detailed credit information along with supplier references.
- Please include a Purchase Order along with Federal Tax ID#, Billing and Shipping address with Contact Name and Phone Numbers.
- International Orders:
- Prepayment via T/T Payment (Wire) or PayPal is required for international orders.
- A Proforma Invoice will be forwarded in advance. Orders will be processed when funds have been fully transferred.
3. What are our shipping options for North America?
4. What are our shipping options for International?
5. How much does shipping cost?
6. Do you offer free shipping?
7. Can I track my order?
Yes, you can track the status of your order in a few ways:
- If you have registered on our website and have an account, you can track your order in the “My Account” section. If your order has shipped, a Tracking # will be listed
- You can always contact your Sales Representative directly (by Phone or email) or @ [email protected]
- If your Order has shipped, you will receive an email notification with a Tracking # for you to Track on the Courier’s Website (for Fedex & UPS).
8. What is our return policy?
New Product Returns require prior approval by Stealth and must be returned within 30 Days of purchase. Each return must be in “as-new” condition and with the original packaging.
- A restocking fee of a minimum 20% may apply. Please visit our Returns and Exchanges page on our website for detailed instructions or contact your Sales Representative.
Returning Products for Warranty
- In the event that a product requires returning to Stealth for warranty work, the customer must first obtain a Returned Material Authorization (RMA) number and clearly mark the RMA# on the exterior of the shipping package.
- The RMA number is valid for 30 days. Stealth will not accept any incoming shipment without an authorized RMA#.
- Stealth is unable to provide loaner units or advance replacements.
Process for Approved Returns
- Contact Technical Support to determine if your product needs to be returned
- Many times our technical support team may be able to assist you via email or over the phone to remedy any issues you may have without your needing to return goods for warranty work.
- You will need to provide the unit’s serial number and your contact information.
- By Phone: (888) 783-2584 or (905) 264-9000 ext #6225
- By web form: Complete the form on Stealth website. Click here to get to the website.
- By e-mail: Send email to this address [email protected]
- Obtaining an RMA Number for Returns
- If it is determined that you need to return the product to Stealth for service please complete our on-line RMA FORM.
- After submitting your information you will receive an email within 24 business hours with the RMA# and detailed instructions on how to return the product.
9. Are there any sales or promotions currently available?
To check for ongoing sales and promotions, please visit our website or subscribe to our newsletter for updates.
10. Can I change or cancel my order after it has been placed?
11. How do I contact customer support for sales and shipping inquiries?
You can reach our Sales Team or your Sales Representative directly by phone Toll Free: 1-888-STEALTH (783-2584); Local; (905) 264-9000 or by email at [Sale contact email address].
11. What should I do if my order arrives damaged or with missing items?
General
1. What does our company do?
Stealth has been offering High-Performance Products and System Solutions for the harshest conditions in the Industrial, Defense, Marine, Transportation, Manufacturing, Emergency Responders, Education & Scientific markets for over 30 years. Our solutions are engineered for real-world infrastructures and trusted by an impressive customer list of Fortune 500s/1000s, Governments, Militaries and Utilities worldwide.
2. How can I contact our company?
You can contact us via Phone, email, Chat or by completing our Contact Form:
- Phone: Toll Free: 1-888-783-2584 or Local: 905-264-9000
- Email: [email protected] or [email protected]
- Chat: Click on the LiveChat icon @ the bottom right of the Website
- Forms: –
Address:
Stealth (Sparton of Canada Limited)
1-7550 Highway 27
Woodbridge, Ontario
L4H 0S2, Canada
3. What are our business hours?
Hours of Operations: Monday – Friday 8:30am to 6:00pm EST
4. Do you have a customer support team?
If you wish to contact our technical support team via e-mail, please fill out the brief form in our Customer Support Section (see Link below). We will do our best to get back to you as soon as we can (usually within 1-2 Business Days).
By Phone – Monday – Friday 8:30am to 6:00pm EST
- Phone: Toll Free: 1-888-783-2584 #6225 or Local: 905-264-9000 #6225
- Technical Support Form: –
Filling out our Form is the best way we can identify your requests and get back to you in a timely manner. Thank you for your understanding, we appreciate your time in submitting this information to us, a good summary of your issues or concerns will help us respond appropriately to your request.
5. How do I place an order?
4 Easy Ways to Order – Orders for Stealth products can be placed directly with Stealth by any of the methods shown below:
- Online: Visit our Online Store and simply add any product found on the website to your cart and then checkout to complete your Order or Quote online.
- Order online and receive free shipping on orders over $995.
- Email: If you would like to place an order by email simply fill out our contact form and a Sales Representative will contact you shortly
- OR
- Submit your Purchase Order directly via email to your dedicated Sales Representative or @ [email protected]
- Phone: Stealth Sales Representatives can take your order from 8:30am to 6:00pm EST, Monday to Friday. Toll Free: 1-888-783-2584 or Local: 905-264-9000
- Fax: submit your Purchase Order to our
- Toll-Free Fax: 1-855-498-1777
- Local Fax: 905-264-7440
- For International customers, same as above except Online
- A Proforma Invoice will be issued in advance for completion of your payment by Wire Transfer.
6. What payment methods do you accept?
We offer you flexibility with the following:
- Credit Card Orders:
- VISA, MasterCard, American Express or PayPal orders are accepted for USA & Canada
- Apple pay, Google pay, Samsung pay and other digital wallets are available online
- Electronic Payments:
- Bank remittances – EFT, ACH or other Wire payment methods are available
- Credit Terms:
- Net 30-Day Credit Terms can be established (North America Only) by supplying detailed credit information along with supplier references.
- Please include a Purchase Order along with Federal Tax ID#, Billing and Shipping address with Contact Name and Phone Numbers.
- International Orders:
- Prepayment via T/T Payment (Wire) or PayPal is required for international orders.
- A Proforma Invoice will be forwarded in advance. Orders will be processed when funds have been fully transferred.
7. What is our return policy?
- New Product Returns require prior approval by Stealth and must be returned within 30 Days of purchase. Each return must be in “as-new” condition and with the original packaging.
-
- A restocking fee of a minimum 20% may apply. Please visit our Returns and Exchanges page on our website for detailed instructions or contact your Sales Representative..
-
Returning Products for Warranty
-
-
In the event that a product requires returning to Stealth for warranty work, the customer must first obtain a Returned Material Authorization (RMA) number and clearly mark the RMA# on the exterior of the shipping package.
-
-
-
The RMA number is valid for 30 days. Stealth will not accept any incoming shipment without an authorized RMA#.
-
-
-
Stealth is unable to provide loaner units or advance replacements.
-
- Process for Approved Returns
-
- Contact Technical Support to determine if your product needs to be returned
- Many times our technical support team may be able to assist you via email or over the phone to remedy any issues you may have without your needing to return goods for warranty work.
- You will need to provide the unit’s serial number and your contact information.
- By Phone: (888) 783-2584 or (905) 264-9000 ext #6225
- By web form: Complete the form on Stealth website. Click here to get to the website. (Insert Technical Support Form)
- By e-mail: Send email to this address [email protected]
- Contact Technical Support to determine if your product needs to be returned
- Obtaining an RMA Number for Returns
- If it is determined that you need to return the product to Stealth for service please complete our on-line RMA FORM.
- After submitting your information you will receive an email within 24 business hours with the RMA# and detailed instructions on how to return the product.
8. Can I track my order?
Yes, you can track the status of your order in a few ways:
- If you have registered on our website and have an account, you can track your order in the “My Account” section. If your order has shipped, a Tracking # will be listed
- You can always contact your Sales Representative directly (by Phone or email) or @ [email protected]
- If your Order has shipped, you will receive an email notification with a Tracking # for you to Track on the Courier’s Website (for Fedex & UPS).
9. Do you offer warranties or guarantees on our products/services?
Yes, our Products come with a Limited Warranty which varies in length by category. An Extended Warranty is also available to purchase for certain products.
- Little PCs / Mini PCs: Standard 2 Years Limited Warranty, extended Warranty available for purchase
- Displays & Monitors: varies by Family
- most are 3 Years Standard Limited Warranty (SV, TT Series)
- some are 1 Year Standard Warranty (SVZ & Specialty Series)
- It is always listed on our Quotes and Website by Product.
- Rack Mount Solutions:
- Rack Mount PCs / Servers are 2 Years Limited Warranty
- Rack Mount KVM / Displays are 2 Years Limited Warranty
- Rack Mount Keyboards are 1 Year Limited Warranty
- Extended Warranty available for purchase on some categories, check with Store or Representative
- Keyboards, Pointing Devices & Accessories:
- 1 Year limited Warranty Standard
You can find our detailed Limited Warranty Policy @ (Insert Link to Limited Warranty)
10. Are there any current promotions or discounts available?
We prefer to be Direct in our approach with Pricing for our Customers, we offer our Best price upfront.
- We do have some items on Liquidation from time to time that offer Discounts (10-50%) on limited items.
- We do offer some limited discounts for larger committed volumes and some of our Approved Partners.
11. How can I become a distributor or partner with our company?
We sell directly around the Globe and do not have any Distributors for our products. We do have Limited Partners and opportunities to Unleash Synergy for Mutual Success !
You can find our criteria and details on our Partnership opportunities in the “Partner Request” section of our Website @ (Insert Link to Limited Warranty)
12. What is our company's commitment to sustainability and the environment?
At Stealth, we recognize the profound impact businesses have on the environment, and we believe in using our influence for positive change. Our commitment to sustainability is not just a statement; it’s a promise to act responsibly, innovate consciously, support our Customer’s environmental requirements and lead by example.
Join us on this journey towards a sustainable and resilient future. At Stealth, we believe that sustainability is a shared responsibility to protect and preserve our planet for generations to come.
We can All make a difference.
13. Are our products/services compliant with industry standards or regulations?
Yes, our Products & Services comply with key industry standards and regulations. We are ISO-9001:2015 certified, it drives our internal processes to ensure consistency, reliability and quality of our offerings. We do offer specific Certifications by Products and all of them can be found in our Product Listings and Descriptions. We also make some of these available to download in our Downloads section of our site (insert link to Download section)
14. Can I request a custom solution or product from your company?
Yes, if you cannot find a Solution that meets your specific needs in our Product Line, we would be happy to discuss your Project with you. We would need you to provide the Specifications you are looking for along with the industry or application you need it for. Our Team will then work with you so assess our capabilities and potential offerings for you. We have 30+ years of experience designing & manufacturing rugged solutions, some of these came from Customer Specific requirements before they became Stand offerings.
You can submit your specifications for your opportunity directly in the “Custom Capabilities” section of our Website @ (Insert Link to Custom Capabilities)
15. How do I report a problem or provide feedback?
If you wish to report a problem, please contact our technical support team. You can reach them via e-mail or phone. Please fill out the brief form in our Customer Support Section (see Link below). We will do our best to get back to you as soon as we can (usually within 1-2 Business Days).
By Phone – Monday – Friday 8:30am to 6:00pm EST
- Phone: Toll Free: 1-888-783-2584 #6225 or Local: 905-264-9000 #6225
- Technical Support Form: (Insert Link to Form Here)
Filling out our Form is the best way we can identify your requests and get back to you in a timely manner.
If you wish to provide us Feedback, feel free to either contact your Sales Representative or submit it to us via email @ [email protected]
We appreciate your time in submitting this information to us, it is one of the best way for us to continue to improve our processes and products for our Customers.
16. What is our company's history and background?
Founded in 1990, Stealth is a leading manufacturer of specialized Rugged Computers, Displays and Peripherals. We are ISO 9001-2015 registered and continually develop innovative products designed to meet the exact needs of our clients. For three decades, we have been providing proven and reliable product solutions assisting our customers with their large variety of applications.
Stealth provides and support High-Performance products and system solutions which can help you meet your computing needs. These Rugged products are designed for the harshest of conditions whether in the industrial, defense, marine, government, utilities or scientific markets. Our Solutions are engineered for real-world infrastructures and trusted by an impressive customer list of Fortune 500’s/1000’s, Governments, Militaries & Utility entities worldwide.
You can learn more about Who is Stealth & our History on our Website by clicking the links.
17. Are there career opportunities at our company?
18. How do you handle data privacy and security?
Stealth wants You to understand how we use the information You provide to us. We take data protection seriously and safeguarding the privacy of customers’ and Website visitors’ is important to us. We have a “Privacy Policy that details how we handle data privacy and security.
This policy sets out the basis on which any personal information we may collect from you, or You provide to us, will be processed and used by us. It also describes how we use cookies and how You can manage them.
We regularly review our policies and any changes will be posted on our Website in the “Legal / Resources” Section under Privacy Policy
19. Can you provide references or case studies of our work?
You can find a number of examples of our work in the Solutions/Applications section of our site. You can get a closer look at our world of rugged innovation and specialized solutions through our Case Studies. Discover how our cutting-edge products have transformed challenges into success stories across diverse industries and applications.
Click here
20. What sets our company apart from competitors?
Stealth offers High-Performance Solutions For Rugged Unpredictability.
We have been offering our Products and System Solutions for the harshest conditions in a variety of difficult Markets. Our solutions are engineered for real-world infrastructures and trusted by an impressive customer list of Fortune 500s/1000s, Governments, Militaries and Utilities worldwide.
Why Stealth ?
Quality / Experience
- Over 30 Years of experience Designing and Manufacturing Quality Solutions that Survive & Perform in the harshest environments.
Product Customization / Development
- Our ability to offer you the options of Built to Order (BTO), Customized Product Configurations, System Integration or Custom Designed solutions that give you the flexibility to get exactly what you need for your applications.
Markets
- Our Products are built with your needs and usage in mind. Our solutions are deployed in a variety of customer critical industries, including Government, Defense, Aerospace, Equipment Automation, Manufacturing, Utilities, Transportation and Marine.
Local Presence and Support
- North American Base
- Lifetime Support
- Availability: Chat / Phone / Web
Contact Us and find out !
Stay Connected
Have questions or need assistance?
Contact us today and discover how our rugged solutions can support your needs.
Stay ahead with the latest innovations—subscribe to our monthly newsletter for news, promotions, and exclusive updates delivered straight to your inbox.